Rodmatic Mill/Turns Compressor Blades Using 'One-Hit' Cycle Technology
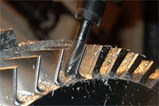
Kent, U.K. - Pre-production samples of a 50 blade compressor turbine blade for a customer in the oil and gas sector are being run off at Rodmatic Hytek of Reading involving four-axis profiling in ‘one-hit' cycles on its Daewoo Puma MS 2000 ST.
Explains Jonathan Imm production manager: "This is a new component for final customer trials that could lead to an important contract. What was important to the customer was that we could produce the 330 mm compressor blade in a single machining cycle using main and subspindle that ensured the relationship of critical features and high levels of concentricity was maintained on the part."
The T6 aluminium compressor blade was machined out of a solid billet with the machine programmed off-line using Pathtrace's EdgeCAM Solid Machinist software. The cycle included extensive roughing and finish machining of bores, faces and spigot diameters plus a wide groove behind the vanes to give clearance for the profile milling of each blade. The Puma was then used in four-axis mode to rough mill slots for the 50 vanes and then each slot was semi-finish and finish profiled slot using a solid carbide ballnose endmill to accommodate the complicated twisted vane profile required by the customer.
Programming took less than two hours to accomplish while the complete machining cycle was just under 4.5 hours for each part. Said director Brian Steatham: "This is the type of work we are gearing up to handle on the international market and are willing to invest in the high technology equipment to achieve the standard of work required and work closely with customers providing a full turnkey solution."
SOURCE: Rodmatic Limited