New Floating Roof Tank Grounding Method Eliminates Rim Fires
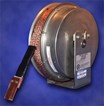
Oil industry engineers must be aware of bound charge and secondary arc risk to oil facilities, since secondary lightning effects such as bound charge and secondary arc can be 1,000 times more common than direct lightning strikes. Bound charge occurs when a storm cell induces an electrical charge on everything beneath it, including metal containers and the flammable product within them, for example, in floating tank storage facilities. Secondary arc, leading to rim fires or explosions, results when the electrical charge differential between a tank wall and its floating roof, rises to the point where the charge can bridge the small air gap between the structures before it can be equalized. A nearby lightning strike, or even filling or emptying a tank quickly, can cause this to occur. The American Petroleum Institute (API) Recommended Practices RP2003 offers more detail on bound charge and secondary arc phenomena, but no practical solution.
The Inadequacy of Shunts for Oil Tank Grounding
Many large crude storage tanks are open without permanently attached roofs. Because each roof floats on top of the product, to prevent vapors from escaping from around the edge of the roof a non-conductive sealing material such as neoprene is generally used. However, the sealing material isolates the roof from the tank wall electrically and from any connection to earth, which poses the danger of rim or other significant fire through the bound charge and secondary arc phenomena.
To overcome this problem the industry usually installs shunts, metal devices attached to the roof so as to be in constant contact with the tank wall regardless of the position of the floating roof. To make contact, shunts are usually made with metal fingers, which are designed to make direct contact with the tank wall. The contact resistance depends on the characteristic of the material used, the contact pressure, and the state of the tank wall.
History has shown that shunts require constant maintenance because:
- 1.Wax and other heavy crude components tend to deposit between the tank wall and the shunt fingers, forming an insulator between them.
2.Since the roof floats, it can easily drift slightly off center and disconnect from the opposite side.
3.The gap between the tank roof and wall is so small that an arc can easily jump that space, and ignite the always present vapor when a charge is on the product. This is often called a "rim fire"; however if the seals are not properly maintained, a conflagration will result.
Ultimately, if the shunts aren't in perfect contact with the tank wall, bound charge will permit an arc to form between them and the tank wall when a storm cell is discharged by a nearby lightning strike. This can lead to rim fires such as the recent ones in Nigeria, and other locations.
Some companies have tried to use long wires that extend from the top of the tank wall down to the center of the floating roof to ground shunts. Worse yet, they extend the wire to one edge of that roof. The impedance of the wire is far too high to discharge a bound charge within the microsecond necessary before secondary arc occurs. The average inductive impedance of these connections can exceed 500 ohms at lightning frequencies.
The requirement is to make a continuous, positive connection between the floating roof and the tank wall, with an impedance low enough to eliminate bound charge risk. However, there are a few problems encountered in trying to make that connection.
The Difficulties of Adequately Grounding
Often, typical two to four-inch wide stainless steel shunts don't actually touch the wall, and others only appear to make a connection. Rust is often found to function as an insulator, too. When measurements of contact resistance are made for these conditions, high resistance or no connection at all is the result.
Other shunts may in fact touch the wall but do so lightly or through a heavy hydrocarbon accumulation on the tank wall. This reduces the shunts' grounding effectiveness to such a degree that many indicate no connection or high resistance when measurements are made.
A new industry trend is to paint the inside of tanks with a non-conductive polymer. Further, to prevent scratching that paint, shunts are often disconnected, and then painted. This does render shunt connections that many look satisfactory, completely ineffective, since that paint is in fact an insulator of high enough resistance to encourage a voltage buildup and subsequent arc.
Alternately, access ramps connecting the top of the tank wall to the roof are often assumed to satisfy grounding requirements, but rust and paint insulate critical joints. Also the wire connection from the tank top to the ramp is typically long and loose with resistance in the range of 500 ohms or more to bound charge current flow.
A Practical Alternative: Using the Storage Tank Itself for Grounding
It is well known and easily proven that any large storage tank possesses the ability to make a solid, low impedance connection to earth without augmentation from external grounding electrodes. The sheer weight of the tank, with or without the product, provides the lowest possible impedance connection to earth. The addition of grounding electrodes provides no measurable influence on the final measurement achieved with the tank alone; unless it rests on a continuous rubber membrane.
Actually, the resistance or impedance to earth is not the problem. The problem is the induced charge on the tank and on the contained product from a storm cell's electrostatic field or that created by rapid flow of product into the tank. This must be quickly removed without causing a fire. Again, it is poor conductivity between the product and conductive container that dangerously inhibits the discharge process.
Since petroleum products are nonconductors, they tend to hold any induced charge. That charge, will slowly migrate toward an attractive conductor of opposite charge, inhibited by the natural impedance of the stored product. The shorter the path to the attractive conductor (in this case, the tank wall), the quicker is the discharge process.
However, the charge near the center of the tank remains much longer, creating concentration of charge in the middle of the tank. The floating tank roof provides an ideal collector/conductor, if there is a connection to the tank wall and earth. Therefore, the roof offers a critical path for the induced charge for the otherwise isolated center of that tank. Obviously, the larger the tank, the more critical this function becomes. Once the charge is collected, it is conducted to the roof edge. If there is no low impedance path between the roof and the wall, secondary arc will occur triggering a fire. If the seals are tight, the fire may not proliferate. However, the risk of a fire is uncomfortably high as statistics indicate.
The Retractable Grounding Assembly (RGA ®) Solution
Making a good connection between the tank wall and the movable floating roof remains the only grounding problem for these storage tanks. Some form of positive connection is required that will bond the two together, independent of the roof position or any seal-related anomalies.
To satisfy this requirement, Lightning Eliminators & Consultants, Inc. of Boulder, Colorado developed the Retractable Grounding Assembly (RGA), a device that provides a direct connection to the tank roof from the tank wall, using a wide, thick-braided wire cable, or strap wound on a heavy stainless steel reel, with tension held by spring loading.
The path of impedance is kept to a practical minimum by the combination of the shortest path, wide braid, and constant tension. The wide braid, also available in nickel-plated copper, for corrosive environments, reduces the "skin effect" at lightning frequencies, and facilitates a tight uniform wind on the reel.
The RGA's design objective was to achieve the lowest possible impedance between the roof and tank wall with minimal maintenance. It is 100% effective, virtually maintenance free, and functions independent of the condition of the tank wall or any shunts. In fact, the RGA works so well it eliminates the need for shunts.
The reel assembly is constructed from 316 stainless steel, with provisions for mounting on the top edge of the tank. There is one model for edge mounting, and another for mounting on the top angle, as a third option it can be mounted on the roof. The flat copper wire end is attached to a roof structure, using several possible options. Since floating roof tanks tend to be of very large diameter, a very large charge can accumulate in the center of each tank. That charge must be carried to the closest location of the tank wall. To assure that path is not too long, for tanks with diameters of 200 feet or more, at least six or eight RGAs may be required. This recommendation is based on the worst case impedance situation, where the tank is nearly empty and the roof is resting on or near the tank floor.
Since the RGA module is designed to be bolted to the top of the tank rim, the location should be chosen so they are in perfect vertical alignment. To install the RGA, it's best to select the anchor point on the roof structure first, and then align the reel assembly so that it's directly above that anchor point. Where more than one RGA is used, they should be evenly spaced around the tank rim. RGAs are currently in use at various locations of Mobil, Chevron, ESSO and Petro de Venezuela (PDVSA) among others.
SOURCE: Lightning Eliminators & Consultants, Inc.