Gas Lift: Adjusting Gas Injection Levels Without Intervention
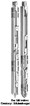
By John Murphy, Houston
Few technologies are as little changed over time as gas lift. Compressed gas injected down the casing-tubing annulus is fed into a fluid column in the tubing to lighten it and allow it to flow upwards to the surface. Innovations such as gas lift valves centralized in the tubing or to the side in side pocket mandrels to regulate gas flow have gone almost unchanged for decades.
But as is the case in so many upstream equipment and practices, subsea and deepwater completions are now driving changes in the staid gas lift technology.
Traditionally, gas lift valves are set in a tubing string via wireline, after the tubing is run and set in the packer. They are equipped, or dressed, with certain choke openings via an orifice insert and fail-closed springs of a certain load that work to regulate the amount of gas allowed into the tubing and when it enters. Since the valves are light and the systems mechanically simple, when changes to these settings are required to fit changing well conditions or because of wear, they are removed, re-worked by changing the orifice or spring size and run back into place simply, quickly, and cheaply on slick line.
Subsea completions, of course, changed that scenario by virtue of the fact that there is no such thing as an inexpensive subsea intervention. In response to this new reality, David Malone, vice president of Schlumberger's Advanced Completions Group, said his company has devised a way to adjust gas injection levels without intervention.
"What we have done is taken the side pocket mandrel that from a functionality standpoint is still like a side pocket mandrel and made a very different device," he said, from his office at Schlumberger's sprawling new research and development center in Rosharon, Texas. "It has a full through-bore, and we have replaced the normally fixed choke with a variable choke that the client can adjust from the surface. They don't have to intervene to change the orifice."
Systems currently in the field, Malone said, are hydraulically operated and can be set from the surface to any of six positions from fully open to fully closed. But electrical versions whose applications will extend back from the high tech world of subsea to dry tree and onshore completions are now in the works.
The advantage of an electrically operated gas lift valve is that its choke size can be infinitely adjusted rather than restricted to some number of specific settings. And that has particular promise for dual completions in which two sets of production strings housed in the same casing are used to drain separate zones. Since they are connected within the system they are nearly impossible to set for optimal efficiency.
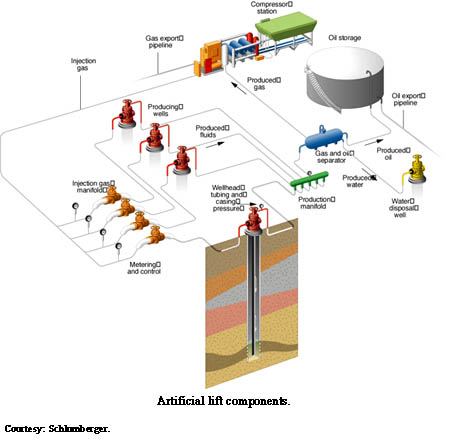
"What happens is since they share the gas from the annulus what you do to one side of the completion affects the other," Malone explained. "Traditionally that meant pulling both valves and trying to adjust them to compliment each other."
Once changes are made to the valves, they are run back in their prospective tubing strings and the well is brought back on production. If the results are less than optimal the operator must do a cost-benefit analysis to decide if the operation is worth repeating. Often operators decide to simply live with what they have rather than risk another intervention that may not significantly help. As Malone put it, "You try but you can never really optimize a dual string gas lift."
With an electrically controlled valve in each side of the dual completion, however, the operator sees immediately the effect of changes made to either well. He can infinitely adjust the two with no intervention cost at all. Also, since the final effects caused by changing gas injection rates can take some time to stabilize, the operator can use as much time as necessary to fine-tune the process, again without cost in either intervention equipment or lost production.
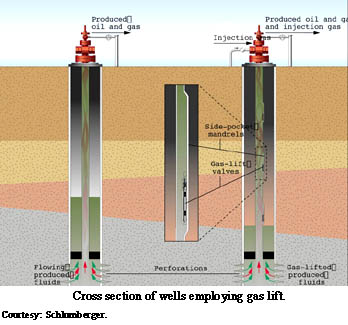
"The market is there for more than subsea," Malone says, "since while non-intervention is important it is more important that [electronic control] is the best way to optimize a dual completion on gas lift."
Norsk Hydro has also combined Schlumberger's smart well technology with gas lift to turn a Norwegian North Sea project doomed by poor economics into a considerable money maker.
The prospect's geology is a familiar configuration of a thin oil rim with a gas cap and water drive. Recovering the highest percentage of oil from such a configuration requires a horizontal well be drilled close to the water contact.
Unfortunately such a completion assures water intrusion early in the well's life, suppressing oil production to beneath the economic limit. Moving the perforation farther from the oil-water contact does not solve the problem either as that would result in another economic liability, that of leaving behind a large percentage of the oil in place.
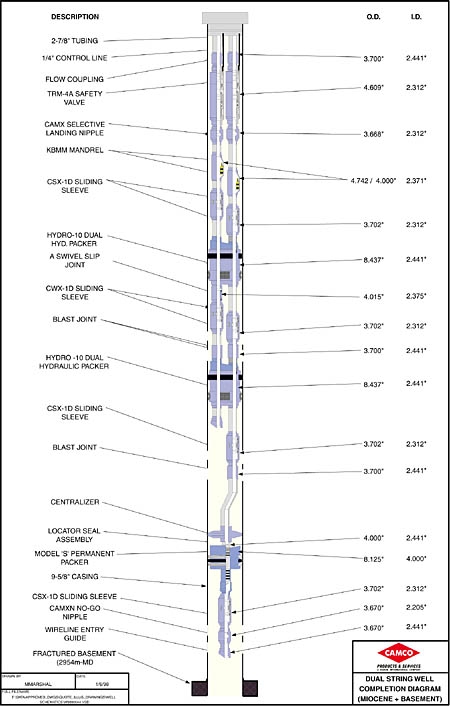
Also, the initial costs of traditional gas injection systems are greatly exaggerated by a subsea completion even before considering the high cost of inevitable numerous interventions. The creative solution to the apparent dilemma of where best to place the perforations came in the form of a blend of gas lift and smart well flow control technology.
First, the company perforated the gas cap in the vertical section above the horizontal well bore. Then the well was completed with an electronically actuated gas lift valve across the gas zone. When the operator begins to see water production, the gas valve will be opened to the appropriate rate so the water can be lifted with the oil rather than instead of it. The economics of such a seemingly basic solution holds significant potential for similar marginal projects.
"It is a very interesting project because before [the installation] the project was not economically practical," Malone said. "But because of this application ultimate recovery will be in the hundreds of millions of dollars. They are the only ones to have done it so far but when you look at it, it is a real winner of an application because you eliminate all the compression infrastructure of a conventional compressed-gas installation."
In a testimony to the technique's success, Norsk has installed the system in five wells, will install seven more in 2000, and will have about 50 in the ground when the project is complete.